
The Oxyfuel Technology
From Chimney to Tank: Unveiling the Journey of CO₂ in the Oxyfuel Process
A groundbreaking shift: The Oxyfuel kiln is transforming cement production by employing pure oxygen instead of ambient air. This alteration in the air supply not only transforms the composition of the exhaust but also facilitates the extraction of CO₂ from the process gas, while concurrently reducing other air pollutants.
Oxygen is essential for the survival of humans and animals, but only a small proportion of what we breathe is oxygen. The air on earth consists of 78 percent nitrogen, 20.95 percent oxygen and the rest are other gasses – amongst other CO₂. When we light a fire somewhere – be it in the fireplace at home, when barbecuing or for combustion processes in large industrial plants – it is the oxygen from this mixture that feeds the fire.
In contrast, Oxyfuel technology introduces pure oxygen into the kiln, fundamentally altering the combustion process and subsequent exhaust emissions. By eliminating ambient air, and consequently nitrogen, from the combustion process, Oxyfuel drastically reduces the production of nitrogen oxides. Conversely, the concentration of CO₂ in the exhaust gas significantly rises, exceeding 90 percent with pure oxygen compared to approximately 15 percent with ambient air. This yields a CO₂-rich exhaust gas, which we call process gas. This is because it is not blown into the atmosphere via a chimney, but is further treated in a complex process.
The elevated CO₂ concentration facilitates the efficient extraction of this climate-altering gas. Through cooling and purification in a Carbon Processing Unit (CPU), the process gas is refined to such a degree that the extracted CO₂ attains food-grade quality, suitable even for beverage production.
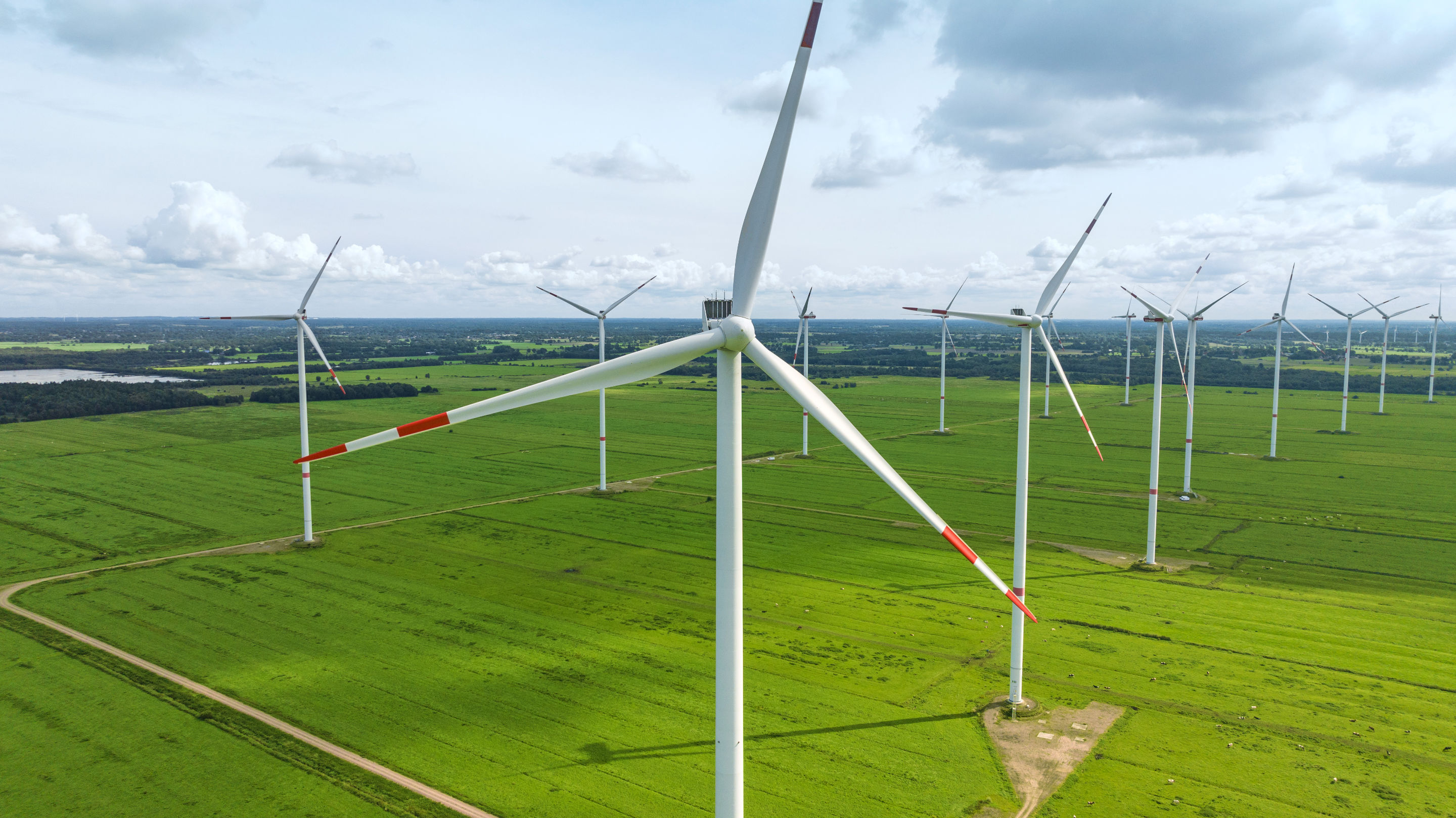
A perfect location for green cycles
Oxyfuel technology is only climate-friendly if it is powered by green electricity. Given its significantly higher energy demands compared to conventional cement kilns, the Lägerdorf site in Schleswig-Holstein emerges as an ideal location. Abundant wind and solar resources in the region ensure a surplus of green energy. We already operate our own wind farm in Rethwisch to supply the Lägerdorf plant. The proximity to the coast also offers good conditions for connecting to offshore wind farms and green electricity supply contracts.
For the cement kiln, we plan to use oxygen generated by various industrial partners in the production of green hydrogen. Water is split into oxygen and hydrogen using a process known as electrolysis. This project is an independent project known as HyScale100. Alternatively, the required oxygen will be provided by an on-site plant.
The production of oxygen and hydrogen for the Oxyfuel process requires renewable energy sources, in line with the overarching goal of climate neutrality. The hydrogen can then also be useful for further utilization of the CO₂. For example, for the production of methanol from CO₂ and hydrogen. Methanol can then be used as a fuel to replace fossil fuels, in sectors such as shipping and aviation.
Holcim, in collaboration with technology partners, is spearheading the establishment of climate-neutral cement plants, integrating Oxyfuel technology and CPU into their operational framework.
With thyssenkrupp Polysius as our plant construction partner, we are developing and building the second-generation Oxyfuel kiln.
Collaborating with the industrial gas specialist Linde Engineering, we are working on the planning of the state-of-the-art CO₂ capture facility, which will purify the processed CO₂ to food-grade quality.
The Oxyfuel process represents a significant milestone in transitioning industrial processes toward environmentally friendly and sustainable production methods. This project serves as a testament to the fact that innovative technologies within the industry not only safeguard the environment but also establish green cycles that unlock fresh opportunities for resource utilization.